Mesin pelet PP adalah salah satu peralatan penting di industri ini daur ulang plastik industri, digunakan untuk mengolah sampah plastik menjadi pelet untuk digunakan kembali. Namun, penggunaan dan pengoperasian dalam waktu lama dapat mengakibatkan mesin tidak berfungsi atau memerlukan perbaikan. Untuk perbaikan mesin pelet ekstruder plastik, berbagai faktor perlu dipertimbangkan, termasuk biaya. Pada artikel ini, kita akan melihat biaya yang diperlukan untuk memperbaiki pelet PP.
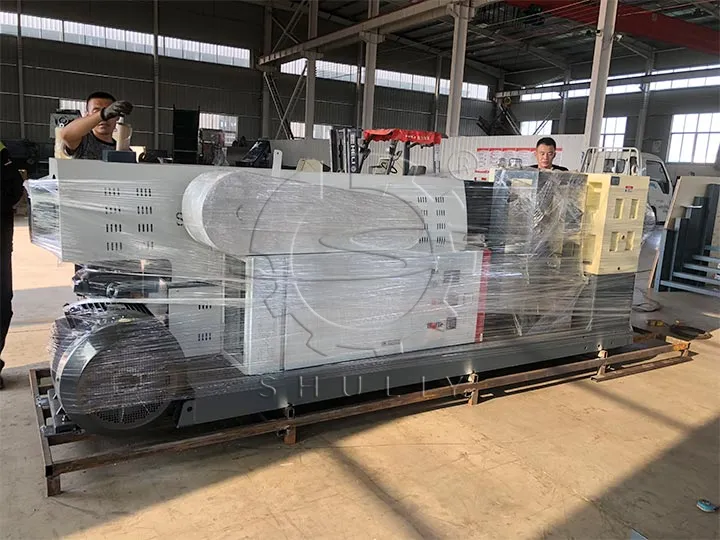
Faktor biaya untuk perbaikan mesin pelet PP
Jenis dan ukuran mesin
Berbagai jenis dan ukuran Mesin pelet PP dapat mempengaruhi biaya perbaikan. Mesin butiran daur ulang plastik kelas industri yang besar relatif kompleks dan mungkin memerlukan tingkat keterampilan personel pemeliharaan yang lebih tinggi dan suku cadang yang lebih mahal.
Jenis kegagalan
Biaya perbaikan tergantung pada jenis kerusakan yang dihadapi mesin pelet PP. Beberapa masalah umum, seperti keausan mekanis, kegagalan sirkuit, atau masalah perlakuan panas, memerlukan metode dan biaya perbaikan yang berbeda.
Biaya suku cadang
Penggantian part atau komponen yang rusak akan berdampak langsung pada biaya perbaikan. Komponen internal granulator plastik mungkin memerlukan penyesuaian khusus atau suku cadang pengganti yang mahal.
Biaya layanan perbaikan
Biaya layanan perbaikan bervariasi menurut wilayah dan penyedia layanan. Tingkat keterampilan dan keahlian yang dibutuhkan juga akan mempengaruhi biaya perbaikan.
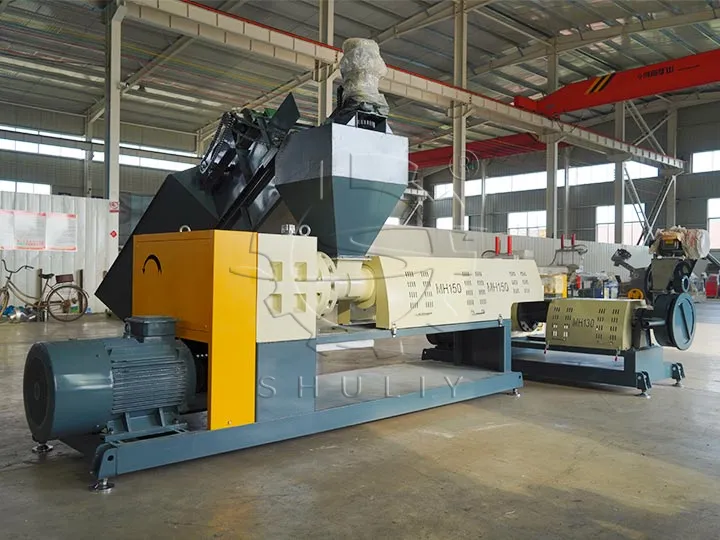
Cara untuk mengurangi biaya perbaikan
- Perawatan rutin: Perawatan dan inspeksi alat berat secara teratur dapat mengurangi kejadian kerusakan mendadak dan menurunkan biaya perbaikan.
- Gunakan suku cadang berkualitas tinggi: Memilih suku cadang berkualitas tinggi dapat memperpanjang umur mesin pelet PP dan mengurangi biaya penggantian suku cadang yang sering.
- Pelatihan personel pemeliharaan: Memberikan pelatihan untuk meningkatkan tingkat keterampilan personel pemeliharaan dapat menyelesaikan masalah dengan cepat dan mengurangi waktu dan biaya yang diperlukan untuk perbaikan.
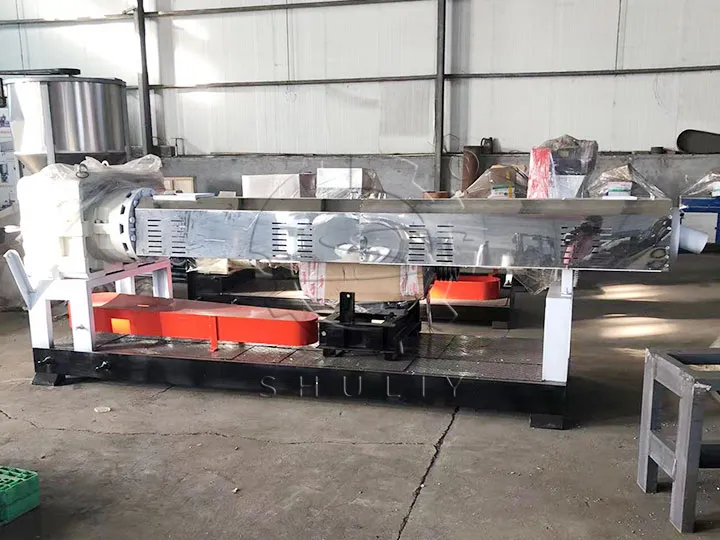