Our plastic friction washer is an efficient equipment designed for PET bottle flake cleaning, which is widely used in waste plastic recycling treatment.
The equipment effectively removes stains, detergents, and other impurities from the surface of bottle flakes through the friction of high-speed rotation, improving the cleaning effect.
The friction washer is usually installed in the process after hot washing or rinsing to further ensure the cleanliness of bottle flakes and provide high-quality raw materials for subsequent recycling processing.
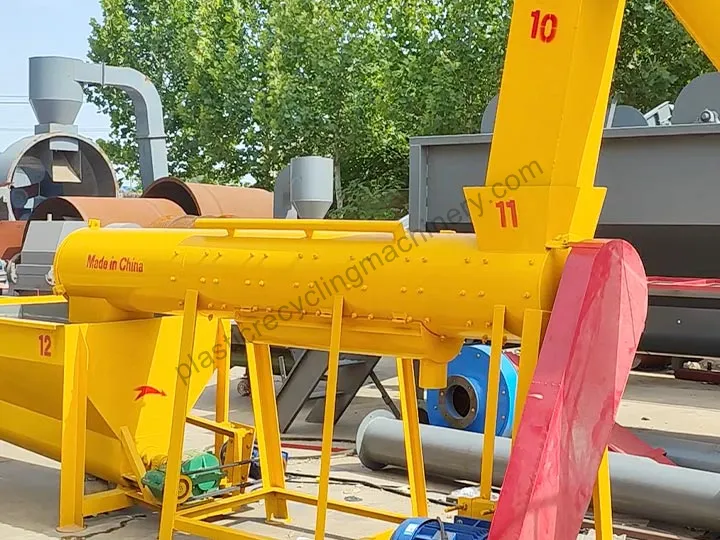
Features of Frictional Washing Machine
- Efficient cleaning: There are several rubbing plates and rubbing strips inside, which can effectively clean the dirt and residue on the surface of PET bottle flakes by strong friction.
- Inclined design: The machine is usually designed to be inclined at 45 degrees for easy drainage.
- Multi-material washing: not only suitable for PET bottle flakes cleaning, but also can clean PP, PE, PVC, and other plastic flakes.
- Customized design: Height and inlet size etc. can be customized according to the customer’s needs, adapting to the existing production line.
Structure of Friction Washer Plastic
The friction washing machine mainly consists of the machine body, frame, motor, feeding port, discharging port, draining port, main shaft, rubbing strip on the main shaft, and rubbing plate on the inner wall of the machine.
The motor drives the spindle to rotate, and the rubbing strips installed on the spindle and the rubbing plates on the inner wall work together to clean the materials by friction efficiently.
The material enters from the inlet, after being scrubbed, it is discharged from the outlet, and the wastewater generated during the cleaning process is discharged through the drainage port. The machine frame firmly supports the whole body to ensure that the equipment remains stable during operation.
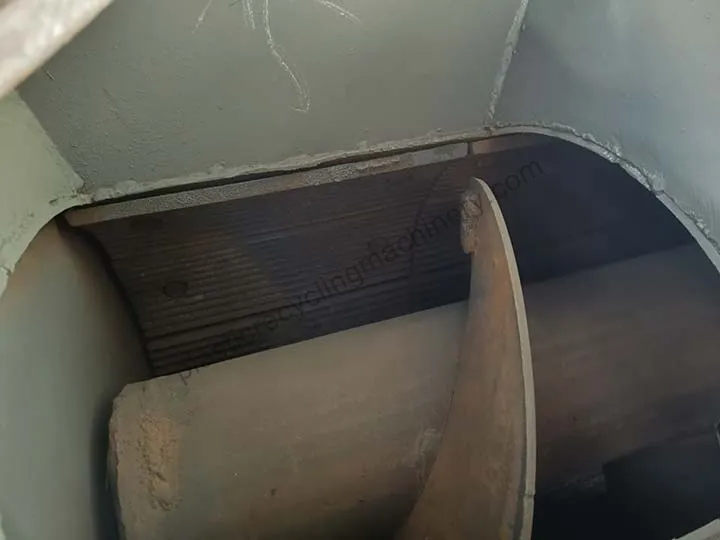
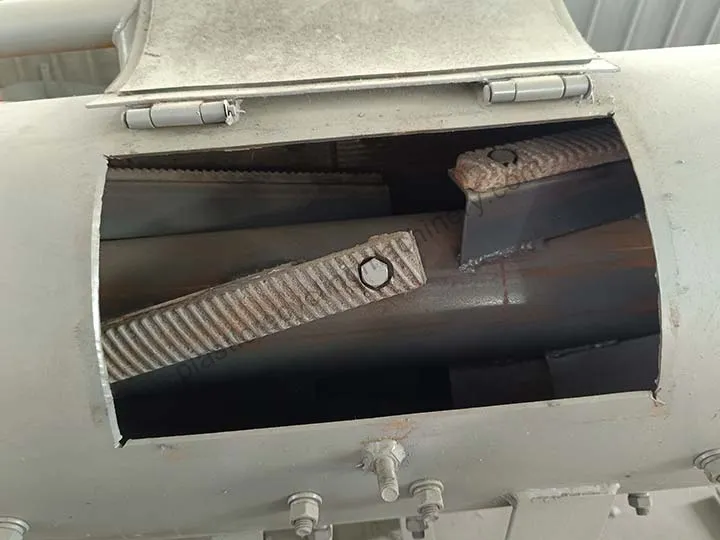
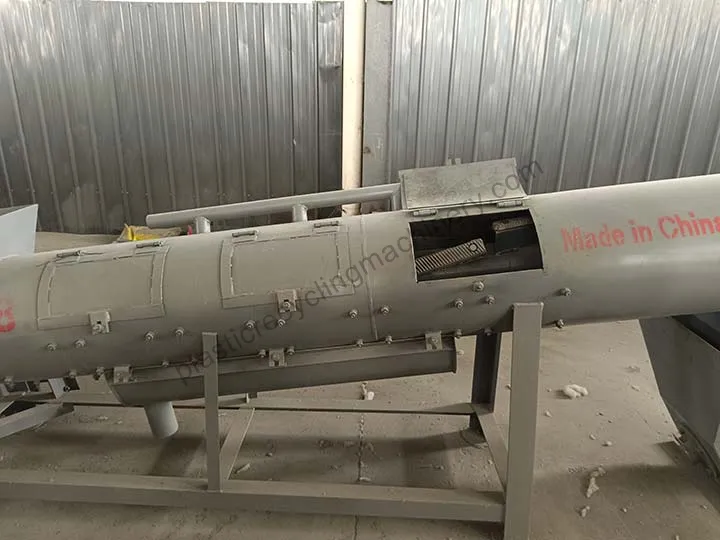
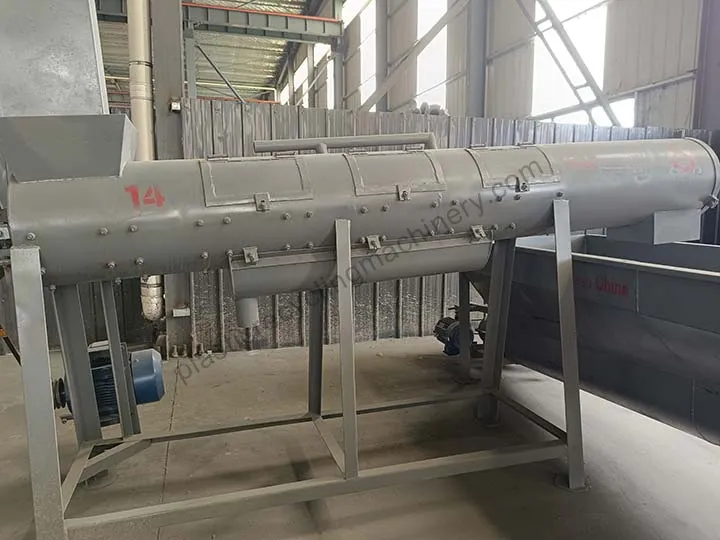
Functions of Friction Washers in Different Positions
Plastic friction washers are usually installed at two key locations in PET bottle washing lines. Firstly, a friction washer plastic recycling can be installed after the sink float plastic separation, which is used to scrub the material in advance to remove surface impurities.
Secondly, a plastic friction washer is needed after the hot wash tank because PET flakes tend to crimp after being heated, resulting in effluent and lye residue. The function of the friction washing machine is to effectively wash out these alkalis, reduce the acidity and alkalinity, and ensure that the cleaned PET flakes achieve a higher degree of cleanliness.
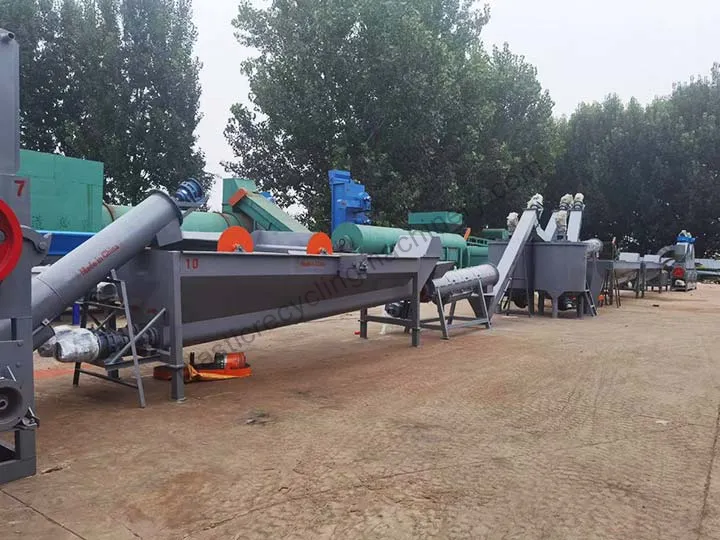
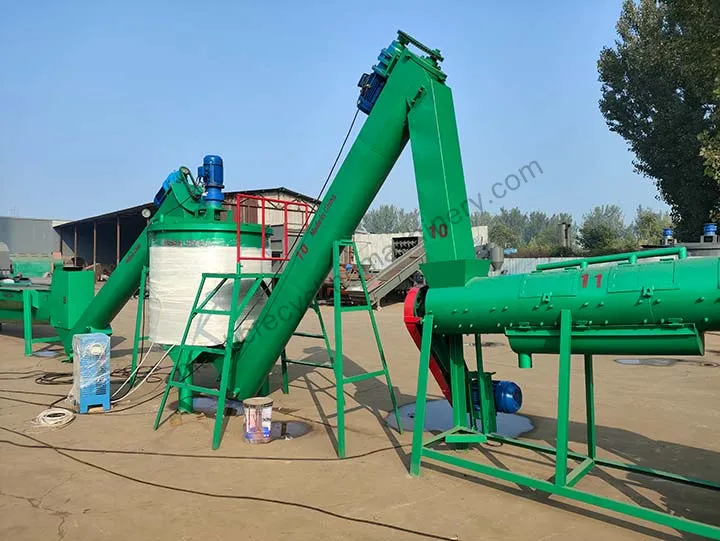
Technical Data of Plastic Friction Washer
- Capacity: 500-1000kg/h
- Length: 3000mm
- Power: 7.5kw
- Out layer: 4mm
- Blade thickness: 6mm
- Capacity: 2000kg/h
- Length: 3500mm
- Power: 15kw
- Out layer: 4mm
- Blade thickness: 6mm
Plastic friction washers are available in a variety of models, these are the models of the Efficient hot sale friction machine. Customers are welcome and encouraged to visit our plastic recycling machine factory to check some of the machines in operation. Please feel free to contact us if you require more detailed information.
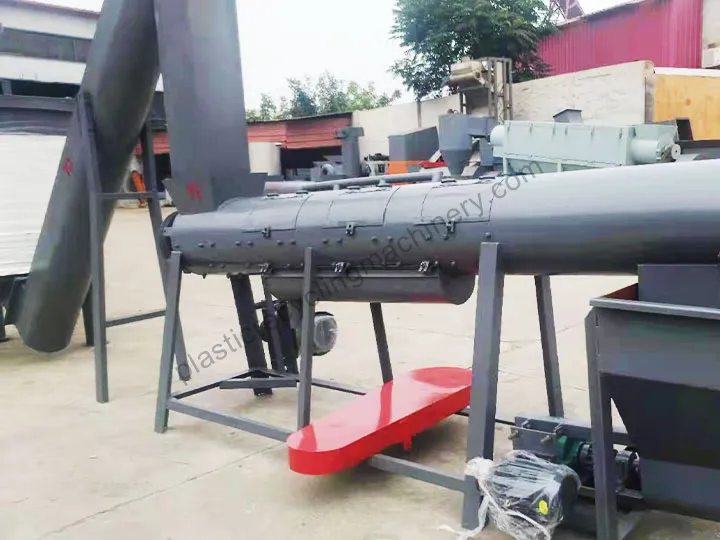
Successful Case of Plastic Bottle Washing Machine
A Nigerian customer has purchased a set of advanced plastic bottle recycling machines including a friction washer plastic recycling from Efficient. These plastic recycling machines not only have efficient washing capacity but also have advanced technology and reliable performance to clean plastic bottles quickly and thoroughly and improve production efficiency.
More details can be viewed: PET Bottle Recycle Machine Assists Nigerian Client to Recycle Bottles
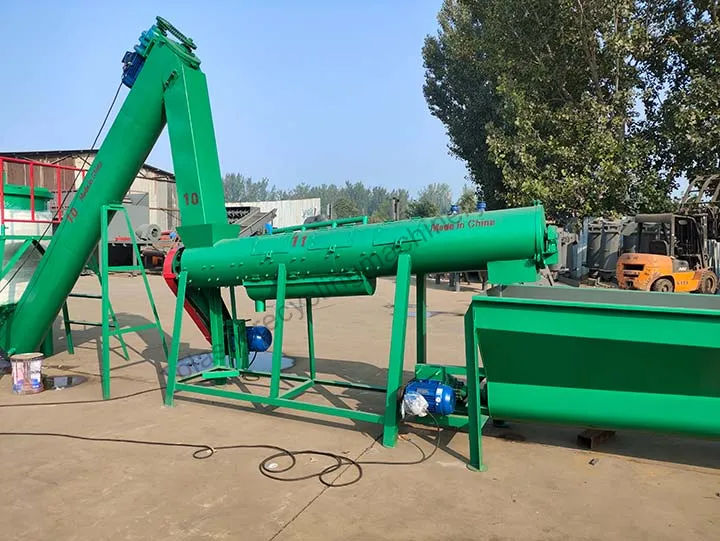
Plastic Friction Washer Price
If you are interested in friction washer plastic recycling, please feel free to contact our sales team for a quote and more details. We offer plastic friction washers in a variety of sizes and configurations to meet the needs of different customers. By investing in this efficient and reliable cleaning equipment, you can bring considerable benefits to the plastic bottle flake recycling process.