In the field of foam plastic recycling, EPS (Expanded Polystyrene) waste poses a challenge due to its large volume and low density, making it difficult to store and transport. As a result, the foam densifier machine plays a vital role in the recycling process. Two commonly used machines are the EPS melting machine and the foam cold compactor. While both aim to reduce volume, they operate on different principles and are suitable for different applications.
This article explains the working principles, advantages, and suitable scenarios for each machine, helping you choose the right equipment based on your specific needs.
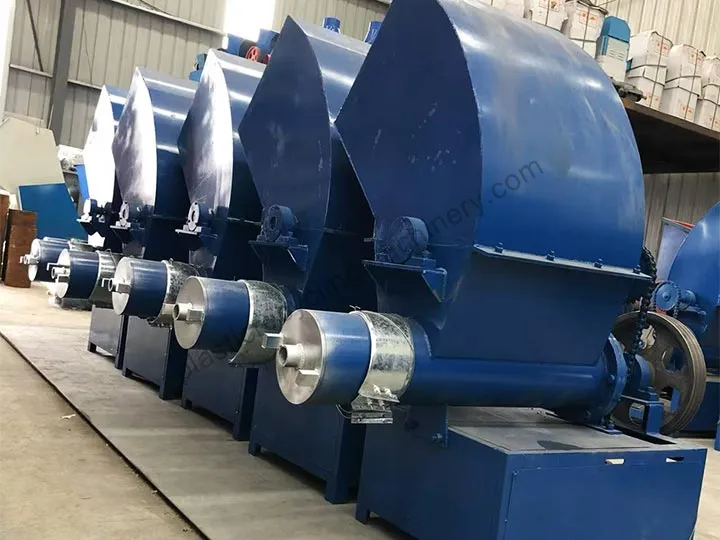
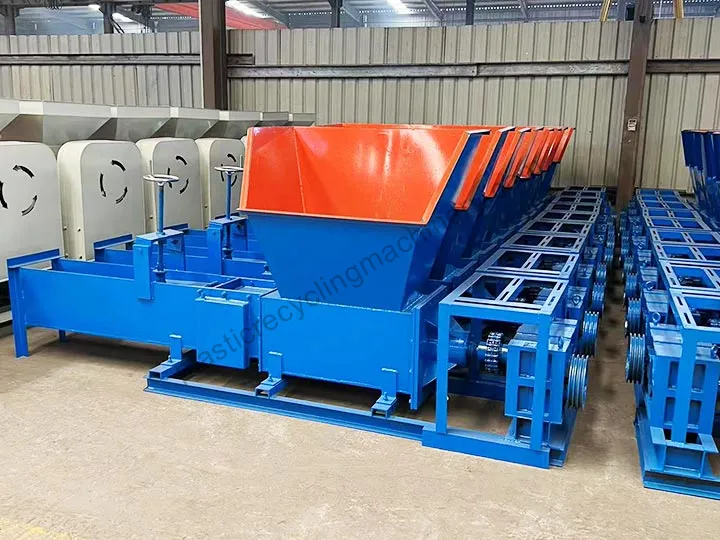
EPS Melting Machine: Working Principle and Features
An styrofoam melting machine uses heat and screw compression to soften waste foam and compress it into dense melted blocks. These compact blocks can be used as raw materials for plastic pelletizing or molding.

Key features of EPS Hot Melting Machine:
- High compression ratio: Reduces volume by 1/50 to 1/90
- Dense output blocks: Easy to stack, store, transport, and sell
- Simple operation: crushing and hot melting in one, save labour

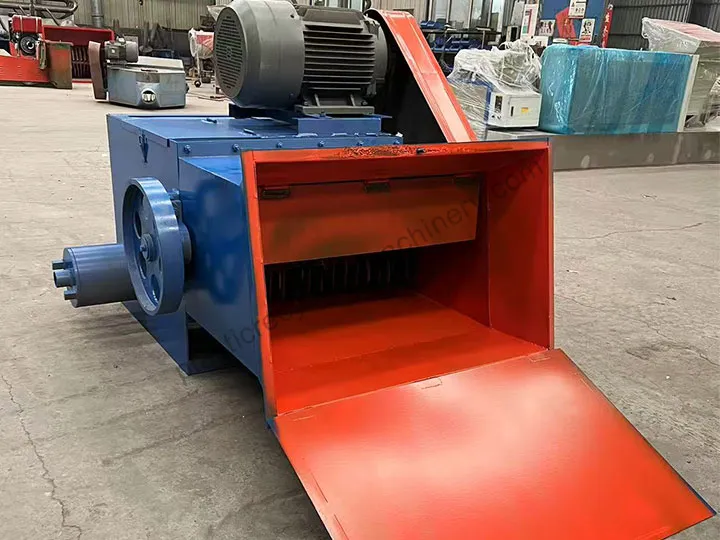
Foam Cold Compactor: Working Principle and Features
A styrofoam compactor compresses foam through mechanical pressure at room temperature, with no heating involved.
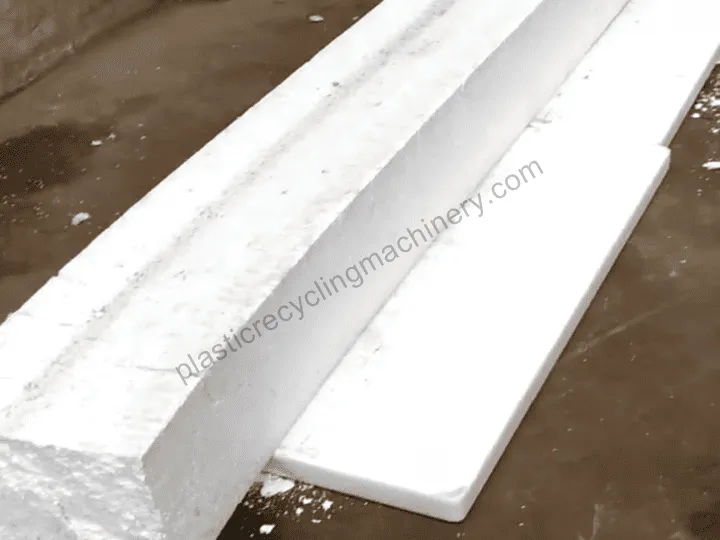
Key Features of EPS Cold Compactors:
- Lower energy consumption: No heating system, reduced power use
- Simple structure: Lower failure rate, easy maintenance
- Lower investment: Suitable for small and medium-sized operations
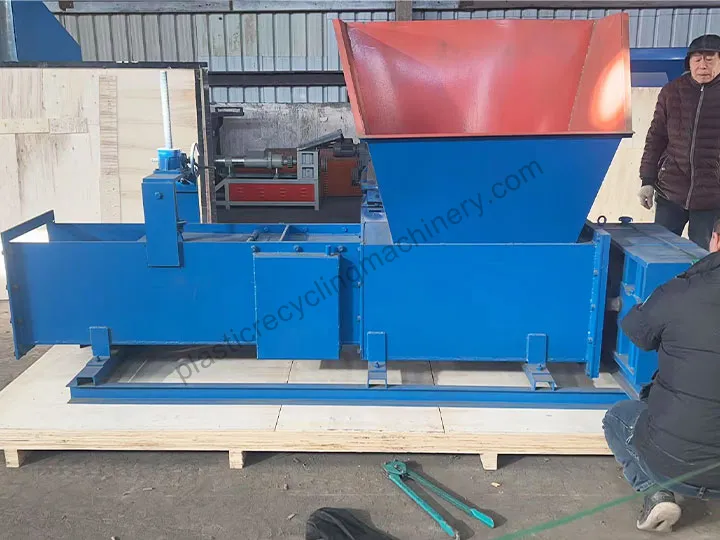
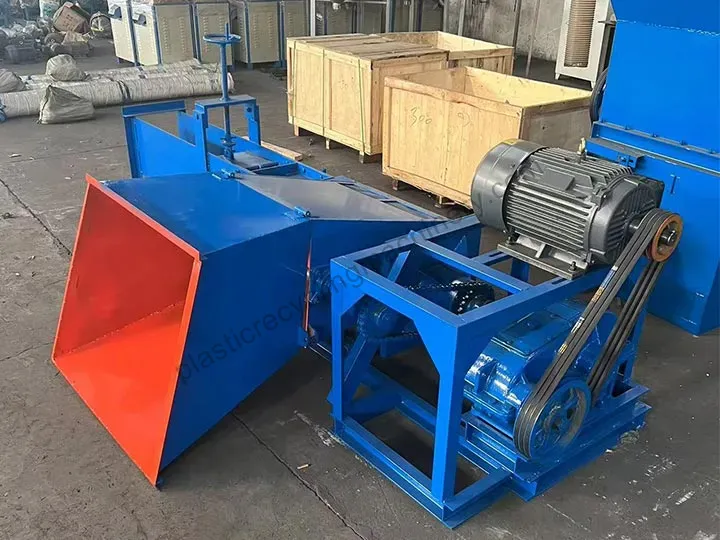
Key Differences Between the Two Types of Foam Densifier Machines
Comparison Item | EPS Melting Machine | Foam Cold Compactor |
Processing Method | Heating + Screw Compression | Mechanical Compression at Room Temperature |
Compression Ratio | Higher (1/50-1/90) | Moderate (1/30-1/50) |
Output Form | Dense melted blocks | Compressed foam blocks |
Energy Consumption | Higher (due to heating) | Lower |
Ideal User | Companies doing pelletizing or reselling melted blocks | Small recyclers focusing on volume reduction |
How to Choose the Right Foam Densifier Machine?
When selecting foam densifier machine, consider the following factors:
- Daily processing capacity: For large-scale operations, melting machines are recommended; cold compactors are more cost-effective for smaller volumes.
- Post-treatment purpose: If blocks will be pelletized or sold, melted blocks are more valuable.
- Energy and budget constraints: Cold compactors are more economical for projects with limited power supply or budget.
- Storage and transport: Melted blocks are denser and ideal for long-distance shipping or export.
- Compression requirement: For users seeking maximum volume reduction, the melting machine is more suitable.
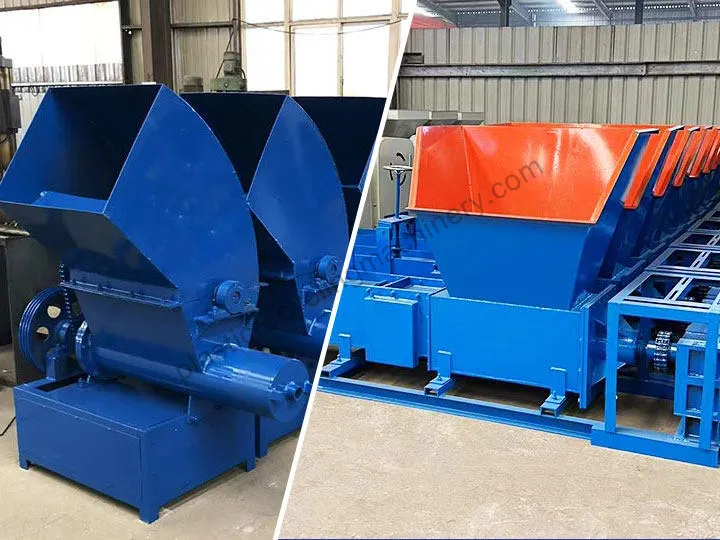
Choose Based on Your Needs to Maximize Recycling Efficiency
There’s no absolute “better” machine—only one that suits your specific requirements. The EPS hot melting recycling machine is ideal for high-efficiency reduction and deep processing, while the EPS compactor is preferred for low energy use and ease of operation.
If you’re unsure which equipment best fits your project, feel free to contact us. We’re happy to offer a tailored solution based on your material type, facility conditions, and production goals.