Plastic bag extruder machine is a key piece of equipment used to convert discarded plastic bags or plastic waste into high-quality plastic pellets. This equipment provides a viable solution for recycling by extruding and heating the plastic material and converting it into pellet form. In the process of producing high-quality pellets, key steps and methods are critical to the quality of the final product.
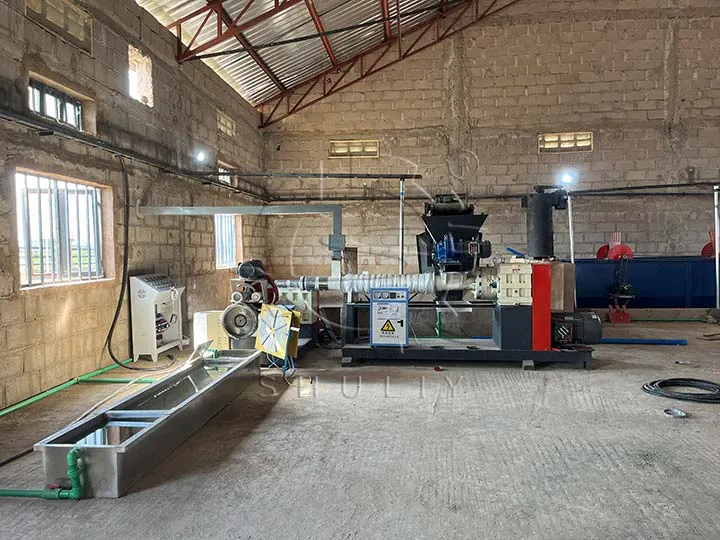
Selection of suitable raw materials
Choosing the right raw material is the first step in producing quality plastic pellets. A good quality raw material ensures the performance and quality of the pellets. Common raw materials include polyethylene (PE), polypropylene (PP) and polyvinyl chloride (PVC). The quality and composition of the raw material will directly affect the quality and use of the final pellets.
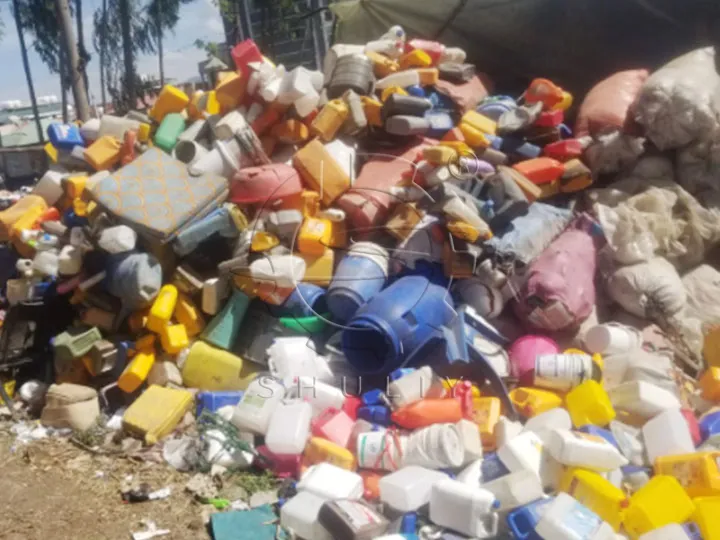
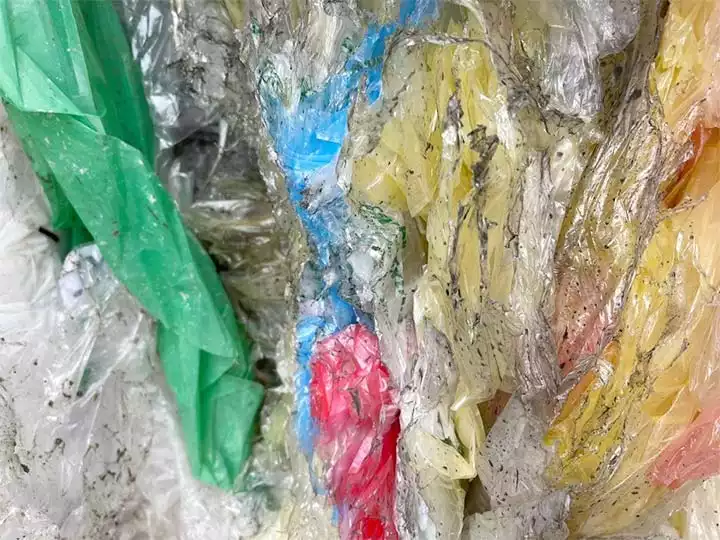
Preparation and handling of raw materials
Before being fed into the plastic bag extruder machine, the raw material undergoes a series of processing steps. This includes cleaning, drying and crushing. Cleaning removes impurities and contaminants and ensures the purity of the pellets. Drying helps eliminate moisture and prevents air bubbles and poor quality during extrusion. Crushing processes the raw material into a pellet size suitable for entry into the plastic bag extruder machine.
Adjusting plastic bag extruder machine parameters
The parameter settings of the plastic bag extruder machine have a direct impact on the quality of the pellets. Reasonable adjustment of film plastic recycling machine parameters such as temperature, pressure, speed, etc. ensures that the plastic pellets remain in a good molten state during the extrusion process and helps to form the pellets uniformly. Depending on the characteristics of the different raw materials, these parameters need to be precisely adjusted to obtain optimum results.
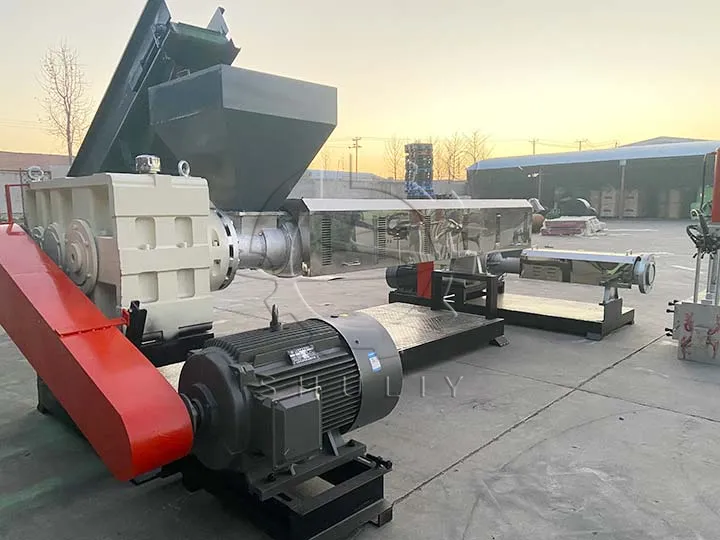
Control of pellet size and shape
Plastic bag extruder machines are able to control the size and shape of the pellets by changing different dies. Choosing the right die will produce pellets that meet specific requirements, such as the diameter, length and shape of the pellets. This step is critical to ensure that the final product meets the customer’s needs.
Implementing quality control and testing
Quality control and inspection is an integral part of the production process. Through the implementation of strict quality control measures, problems in production can be detected and corrected promptly to ensure the consistency and quality stability of the pellets. Various testing methods, such as appearance inspection, size measurement and chemical composition analysis, are used to ensure that the pellets meet the standards and specifications.