Plastic foam extruder is a commonly used equipment for making foam pellets from plastic foam by melting and extruding. However, in the process of use, various faults may occur, affecting production efficiency. Several common faults and corresponding solutions will be introduced below.
Uneven quality of recycled pellets
Recycled foam particles have different sizes and uneven density during the production process, which affects the quality of the product.
Solutions
- Check the raw materials: Make sure the quality and proportion of raw materials are correct, and avoid mixing different materials resulting in uneven quality of pellets.
- Adjust the temperature and pressure: Adjust the temperature and pressure of the plastic foam extruder appropriately to ensure that the foam material is fully melted and evenly distributed.
- Clean the molds and equipment: Clean the surface of the molds and plastic foam extruder to prevent the residue from affecting the shape and quality of the granules.
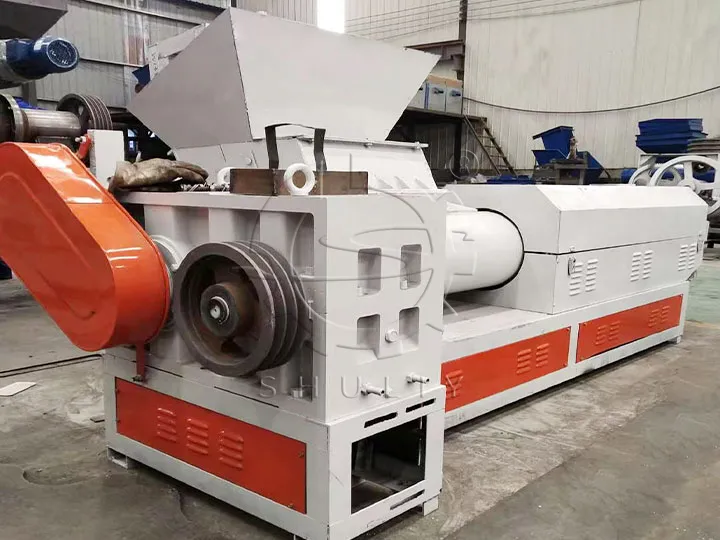
Plastic foam extruder clogging
Extruded foam plastic may be clogged with pipes or feed ports, resulting in production interruption.
Solutions
- Stop and check: Check the pipes and feed inlet in time to clear the clogging under the stoppage condition.
- Use appropriate raw materials: Avoid using too large or too small raw materials to prevent clogging.
- Regular maintenance: Clean and maintain the extruded foam plastic regularly to prevent clogging.
Foam granulator noise abnormality
EPE styrofoam pelletizing machine produces abnormal noise during operation, beyond the normal range.
Solutions
- Check the mechanical parts: Check the various parts of the plastic foam extruder, including bearings, transmission devices, etc., exclude damaged or worn parts, and lubricate or replace them.
- Tighten loose parts: Check the screws, nuts, and other parts of the extruded foam plastic to make sure they are tightened securely to minimize the mechanical vibration caused by the noise.
- Maintaining the noise reduction device: Check that the noise reduction device is working properly and carry out the necessary cleaning and maintenance.
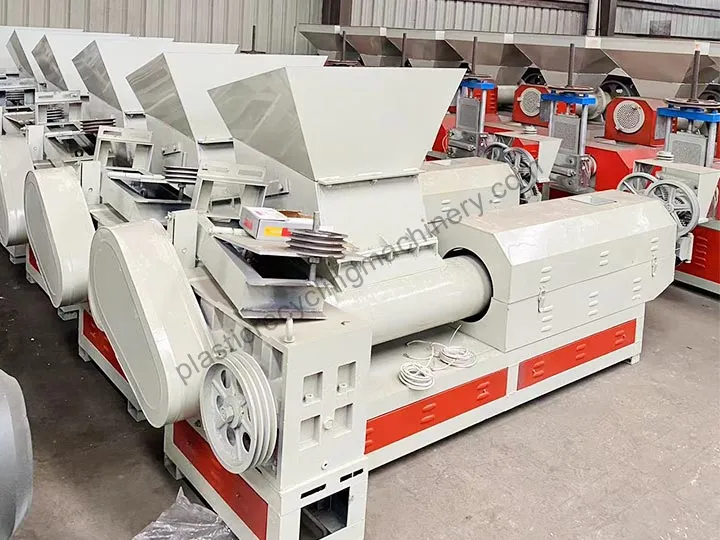
Wear and tear of mechanical parts
After a long time of use, the mechanical parts of the plastic foam extruder, such as molds, screws, etc., may be worn out, affecting the production efficiency and product quality.
Solutions
- Regular inspection and lubrication: Regularly check the wear and tear of mechanical parts, and carry out timely lubrication and maintenance to prolong the service life.
- Replacement of worn parts: Once serious wear is found, replace the damaged mechanical parts in time to ensure the normal operation of the plastic foam extruder.
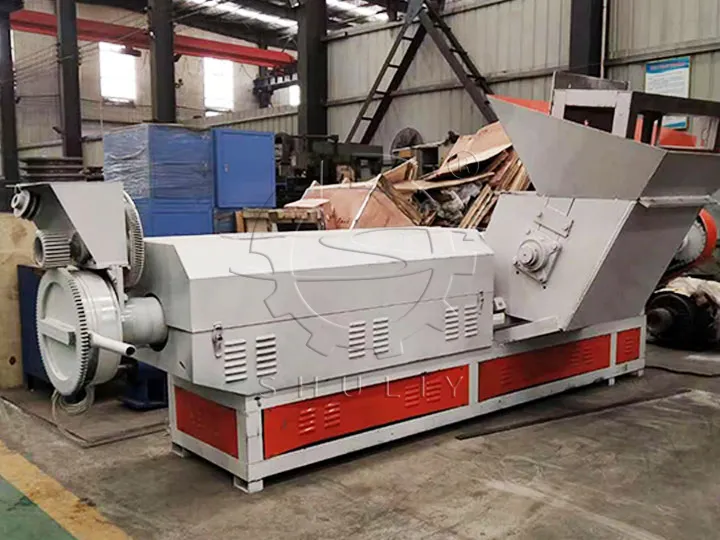