The plastic pellet extruder machine, as one of the commonly used equipment in plastics processing, plays a key role in the plastic pellet molding process. The net (also known as a strainer) in its die head is an important part of ensuring the quality of the molded plastic pellets.
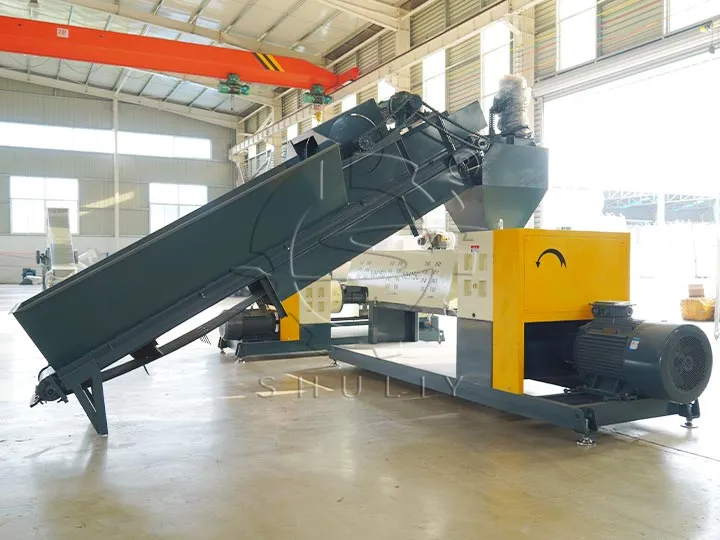
Die head mesh and its function in the extruder
Function of the die head in plastic pellet extruder machine
The die head of plastic granulator machines is a component used to heat, melt and extrude plastic pellets through a specific shaped orifice. Its design shape and aperture size have a direct impact on the quality of the molded product.
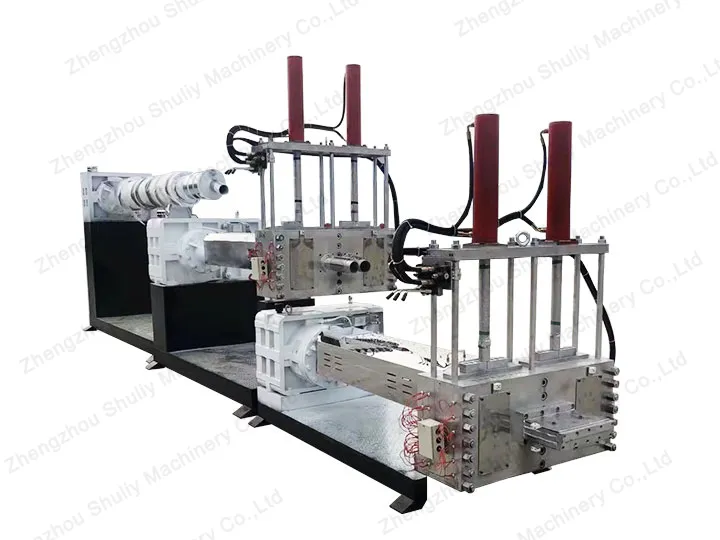
The role of mesh in the die-head
Mesh is often used inside the die head to filter out impurities and ensure that the molten plastic particles are not affected by the impurities, thus ensuring the quality of the finished product. The role of mesh is similar to that of a filter, effectively blocking foreign objects from entering the die head orifice to ensure the cleanliness and quality of the product.
Die head mesh replacement frequency
Change frequency depends on the cleanliness of the material
The dirtier the material, the more frequently the die mesh needs to be changed. Some plastic pellets may contain impurities, uneven particles, etc., which will cause the die head mesh of the plastic pellet extruder machine to be damaged or clogged more quickly, affecting the extrusion molding results. In this case, it is recommended that the die head mesh of plastic pellet extruder machine be changed promptly according to production needs to ensure product quality.
Comparatively speaking, if the material is cleaner, the frequency of die-head mesh of plastic pellet extruder machine replacement can be moderately extended. In general, clean plastic pellets may be able to meet the production demand by replacing the die head mesh once a week.
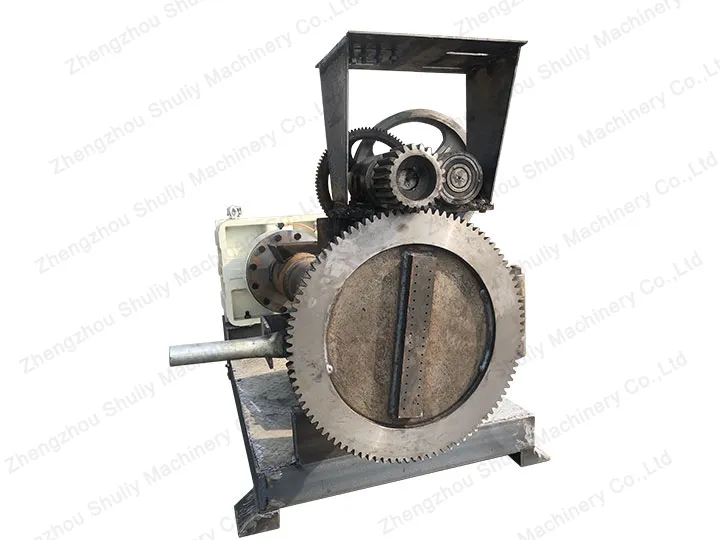
Replacement process and reuse
The replaced die head mesh of plastic granulator machines can be cleaned and treated so that it can be reused. It is common practice to remove residue from the mesh by fire grilling, chemical cleaning, etc. to ensure that the mesh surface is free of contamination and ready for reuse.
However, it is important to note that reused mesh needs to undergo a rigorous cleaning process to ensure that it does not introduce impurities or contamination to the next production process.
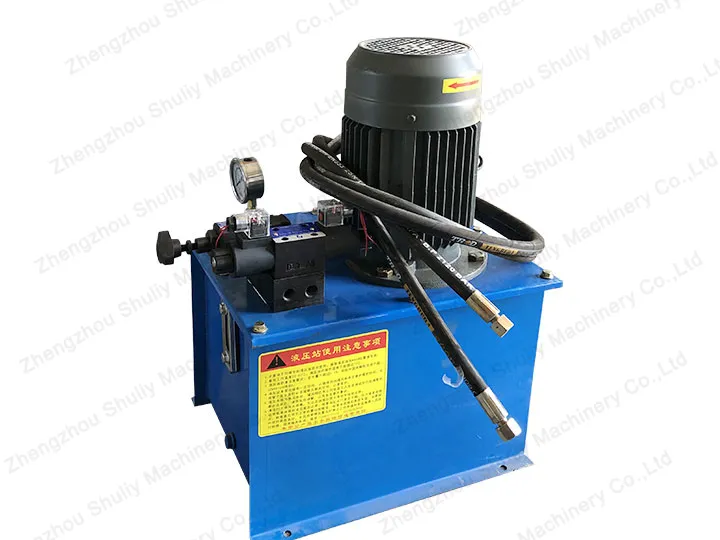